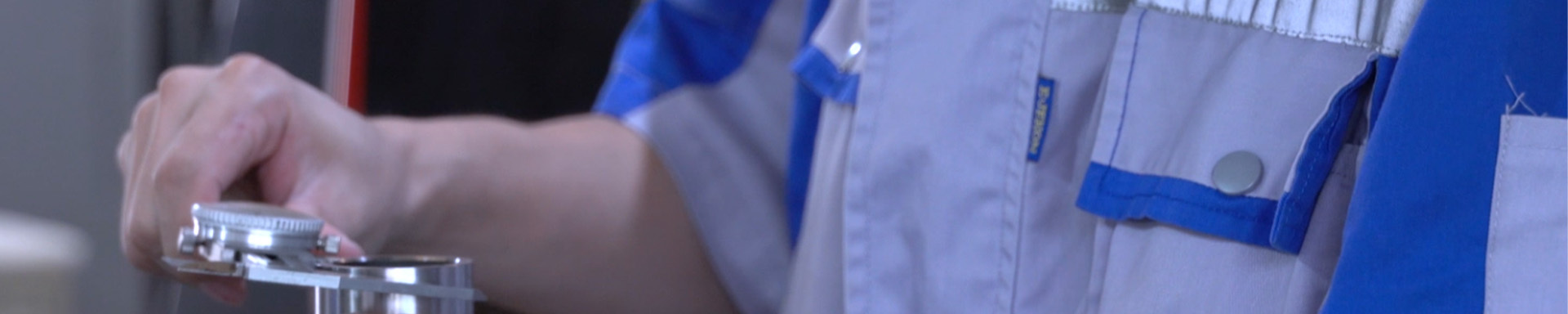
Стеллит 21 / AMS5385G UNS R30021
2021-09-06 10:52Сплав Stellite 21 CoCrMo (кобальт-хром-молибден) является одним из сплавов на основе кобальта, а также разновидностью так называемого сплава стеллита. Это сплав на основе кобальта с превосходной износостойкостью и коррозионной стойкостью. Первым сплавом на основе кобальта был бинарный сплав кобальт-хром, затем из него была получена тройная композиция кобальт-хром-вольфрам, а затем был разработан сплав кобальт-хром-молибден. Кобальт-хром-молибденовый сплав - это сплав с кобальтом в качестве основного компонента, содержащий значительное количество хрома, молибдена и небольшое количество никеля, углерода и других легирующих элементов, а иногда также содержащий железо. В зависимости от состава сплава из них можно производить сварочную проволоку, порошок можно использовать для сварки твердых поверхностей, термического напыления и т. Д.
Кобальт и хром являются двумя основными элементами сплавов на основе кобальта, и добавление молибдена может привести к получению более мелких зерен и более высокой прочности после литья или литья. Кобальт-хром-молибденовые сплавы в основном делятся на две категории: первая - это сплавы CoCrMo, которые обычно представляют собой литые изделия, а другая - сплавы CoNiCrMo, которые обычно подвергаются прецизионной обработке (горячее литье). Литой сплав CoCrMo использовался в стоматологии на протяжении десятилетий и теперь используется для изготовления искусственных суставов. Литой сплав CoNiCrMo используется для изготовления суставов, выдерживающих большие нагрузки, таких как коленные и тазобедренные суставы. Однако в качестве материала суставного имплантата сплав CoCrMo будет выделять Co, Cr, Ni и другие вредные ионы после имплантации в человеческое тело.
Химический состав Стеллита 21:
Механические свойства Стеллита 21:
Анализ свариваемости
Согласно имеющемуся международному опыту, функция наплавочного слоя в основном определяется химическим составом и степенью разбавления наплавленного металла наплавочного слоя, а химический состав наплавленного металла зависит от химического состава сварочного материала. . Когда выбирается сварочный материал. После этого химический состав металла шва был в основном подтвержден. При выборе процесса сварки необходимо учитывать недопущение того, чтобы внешние факторы вызывали изменения химического состава металла шва или проникновение других примесных элементов; величина степени разбавления зависит от величины подводимого тепла (E) во время сварки, то есть тепла. Чем больше подвод, тем выше степень разбавления; в противном случае уменьшение и подвод тепла рассчитывается следующим образом:
В формуле: E - погонная энергия сварки, Дж / мм; I - сварочный ток, А; U - сварочное напряжение, В; u - скорость сварки, мм / мин. Поэтому при выборе процесса сварки необходимо обеспечить химический состав металла шва наплавочного слоя и снизить количество подводимого тепла при сварке. Предварительно подтвержденный путь технологического процесса выглядит следующим образом: вырубка → строгание и неразрушающий контроль фрезерования (PT) → предварительный нагрев → сварка → визуальный контроль → неразрушающий контроль (PT) → обработка образцов → химический анализ и функциональные испытания → сбор материала → анализ результатов. → Отчет об очистке и использовании производства (5) 0
Требования перед сваркой
После проверки поверхности наплавочной сварки на отсутствие трещин, пор, прослойки, толстой кожи и других поверхностных дефектов посредством проверки на пропитку жидкостью, очистите поверхность наплавочной сварки ацетоном. Для наплавки качественных материалов предварительно нагрейте наплавленные детали до температуры выше 15 ° C. После того, как рука коснется и станет теплой, сразу же начнется сварка. В то же время убедитесь, что относительная влажность окружающей среды при сварке не превышает 80%, скорость ветра не превышает 2 м / с, а чистота газа Ar должна достигать 99,99%.
Требования при сварке
Из формулы расчета можно узнать, что величина подводимого при сварке тепла (E) пропорциональна величине произведения сварочного тока (I) и сварочного напряжения (U), а также величине скорости сварки ( v) обратно пропорционально. Для метода ручной аргонно-дуговой сварки (GTAW) неплавящимся электродом сварочный ток относится к предварительно установленным управляемым элементам, а сварочное напряжение и скорость сварки относятся к искусственному управлению и случайным элементам. Это четвертая часть французской спецификации RCC-M. Цитируется в томе S"Сварка". В то же время это описано в пункте 8.5.4 ISO 15614-7: 2007."Аттестация процедур сварки металлических материалов, часть 7: наплавка": Верхний предел утвержденного диапазона погонной энергии для каждого слоя выходит за рамки оценки процедуры сварки. Тепловложение, используемое тем же слоем, составляет 25%, а нижний предел составляет менее 10% подводимого тепла, используемого тем же слоем, при оценке процесса сварки.
Поскольку сварочное напряжение и скорость сварки контролируются людьми, при выборе параметров сварки приоритетным является контроль величины сварочного тока. Исходя из предпосылки обеспечения качества наплавочной сварки, выбирайте как можно более низкое значение сварочного тока, а именно:"малый ток, сварка короткой дугой, быстрая многослойная многопроходная сварка". Регулировка параметров спецификации сварки. Во время наплавки строго контролировать расстояние между валиками. Следующую полоску следует прижать к половине ширины предыдущей, чтобы минимизировать степень разбавления. Направление сварки между сварочными проходами следует сваривать взад и вперед один за другим, чтобы уменьшить сварочное напряжение и деформацию. Перед сваркой источник сварочного тока должен быть настроен заранее на состояние защиты предварительно подаваемого газа аргона и газа, подаваемого с задержкой аргона. Вначале следует отрегулировать ток на плате зажигания дуги из того же материала, дугу следует зажечь, а затем переместить сварку в начало зоны сварки, чтобы начать сварку. Начиная с пронумерованной позиции № 6 вдоль центральной оси сварного шва, сварной шов сваривают вперед и назад с обеих сторон. Кратер необходимо заполнить при закрытии дуги, чтобы предотвратить образование кратерных трещин. Сварочные соединения используют метод дуги оплавления для обеспечения качества соединений на сварных соединениях. Сварные швы между каждым сварочным проходом необходимо располагать в шахматном порядке. Толщина наплавки должна быть в пределах 3,5 ~ 4,0 мм. После сварки используйте минеральную вату, чтобы согреться и медленно охладить до комнатной температуры.
Недостатки и меры сварки
Обработка внешнего вида до и во время сварки. Тщательно удалите оксидную окалину с поверхности, масляные пятна, загрязнения, межслойные покрытия, расплавленный шлак и другие вредные примеси, чтобы поверхность покрытия была гладкой и смазанной, с металлическим блеском и без дефектов, таких как трещины, поры, включения шлака и т. Д. на поверхности;
Контроль температуры во время сварки, включая предварительный нагрев перед сваркой, контроль температуры между проходами и медленное охлаждение после сварки. Предварительный нагрев перед сваркой и медленное охлаждение после сварки могут снизить скорость охлаждения после сварки и уменьшить часть остаточного напряжения, вызванного опасным температурным градиентом; контроль межслойной температуры может сократить время пребывания при высокой температуре, предотвратить охрупчивание сварного соединения крупными кристаллами и снизить ударную вязкость;
Термическая обработка для снятия напряжений после сварки. После завершения наплавки внутреннее напряжение удержания велико, что просто вызывает растрескивание. Благодаря термообработке для снятия напряжения внутреннее напряжение может быть устранено вовремя, чтобы предотвратить возникновение дефектов.